Diagram |
Description |
Calculation formula of moment of inertia |
Rotation radius |
Diagram |
Description |
Calculation formula of moment of inertia |
Rotation radius |
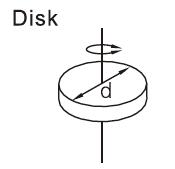 |
d: Diameter (m) m: Mass (kg) |
 |
 |
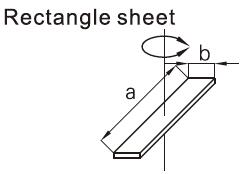 |
a: Sheet length (m) b: Length of side (m) m: Mass (kg) |
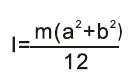 |
|
Note: no special installation direction |
Note: no special installation direction |
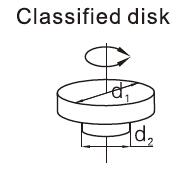 |
d1: Diameter (m) d2:Diameter (m) m1: d1 Mass (kg) m2: d2 Mass (kg) |
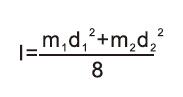 |
 |
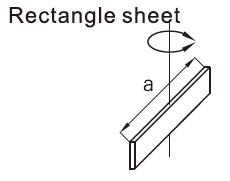 |
a: Sheet length (m) m: Mass (kg) |
 |
 |
Note: Compared with d2, disregard d1 if d1 is extremely tiny |
Note: no special installation direction |
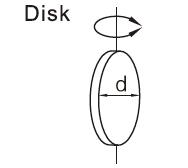 |
d: Diameter (m) m: Mass (kg) |
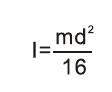 |
 |
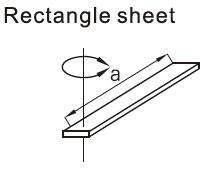 |
a: Sheet length (m) m: Mass (kg) |
 |
 |
Note: no special installation direction |
Note: 1. horizontal installation. 2. pay attention to the change of movement time in case of vertical installation. |
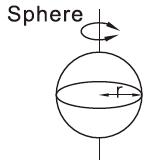 |
r: Radius (m) m: Mass (kg) |
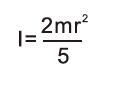 |
 |
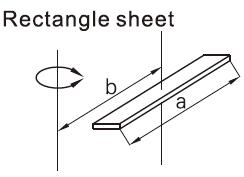 |
a: Sheet length (m) b: Distance between the rotation axis and the gravity center of loading (m) m: Mass (kg) |
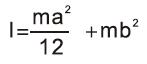 |
 |
Note: no special installation direction |
Note: the cuboids are the same. |
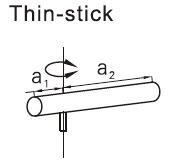 |
a1: Sheet length (m) a2: Sheet length (m) m1: a1 Mass (kg) m2: a2 Mass (kg) |
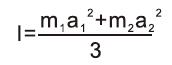 |
 |
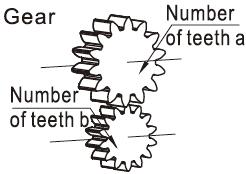 |
a: Tooth number of gear b: Tooth number of loading gear |
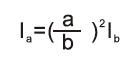 |
|
Note: 1. horizontal installation. 2. pay attention to the change of movement time in case of vertical installation. |
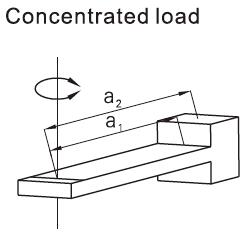 |
a1: Vertical distance between the rotation axis and the concentrated loading (m) a2: Length of arm (m) m1: Mass of concentrated loading (kg) m2: Mass of arm (kg) |
 |
|
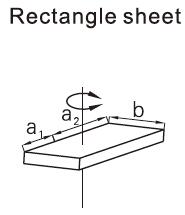 |
a1: Sheet length (m) a2: Sheet length (m) b: Length of side (m) m1: a1 Mass (kg) m2: a2 Mass (kg) |
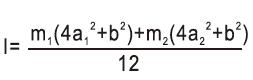 |
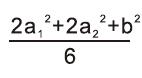 |
Note: 1. horizontal installation. 2. compared with m, disregard if m is extremely tiny. 3. calculate K according to the shape of concentrated loading row by row. For example, when the loading is spheroid, K=2r²/5 |
Note: 1. horizontal installation. 2. pay attention to the change of movement time in case of vertical installation. |