200 watt 24V DC servo motor with low cost, 1500 rpm rated speed, no-load speed up to 1700 rpm, 1.27 Nm rated torque and peak torque up to 3.8 Nm, feedback with 2500 PPR incremental encoder. ATO powerful DC servo motors features of low rotor inertia, high torque density, high peak torques, low noise, low temperature rising, lower current consumption.
Basic Specifications
- Model: ATO-80AS0202-15
- Rated Power: 200W
- Rated Voltage: 24V DC
- Rated Current: 9.4 A
- Rated Torque: 1.27 Nm
- Peak Torque: 3.8 Nm
- Rated Speed: 1500 rpm
- No-load Speed: 1700 rpm
- Working Efficiency: 85%
- Flange Size: 80mm
- Weight: 2.5 kg
Technical Parameters
- Incremental Encoder Line: 2500 PPR
- Rotary Inertia: 418 Kg.m2x10-6
- Line Resistance: 0.06 Ω
- Armature Inductance: 280 μH
- Torque Constant: 0.17 Nm/A
- Brake Apparatus Voltage: 24V DC, brake release when powered
- Motor Lead Length: 1 meter
- Back EMF: 17.3 vkr/min
- Protection Grade: IP55
- Insulation Class: Class F
- Certification: CE, ISO
Features
- 200W DC servo motor with IP55 protection grade and F class insulation structure
- Optimized winding end structure, minimized copper loss and iron loss, small size, light weight, low temperature rise and high efficiency (85%)
- Super coercivity, ATO DC brushless servo motors using NdFe35 permanent magnet material, strong anti-demagnetization ability, stable motor performance
- Low noise, low vibration, low moment of inertia
- High torque, fast dynamic response, wide speed range, strong overload capacity (4 times)
Dimension (Unit=mm)
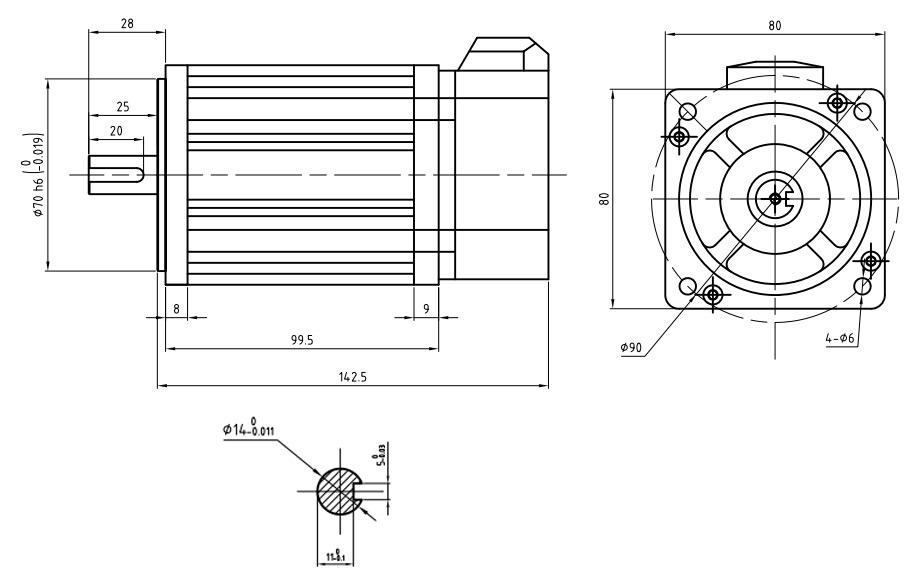
Wiring Definition

Speed-Torque Curve
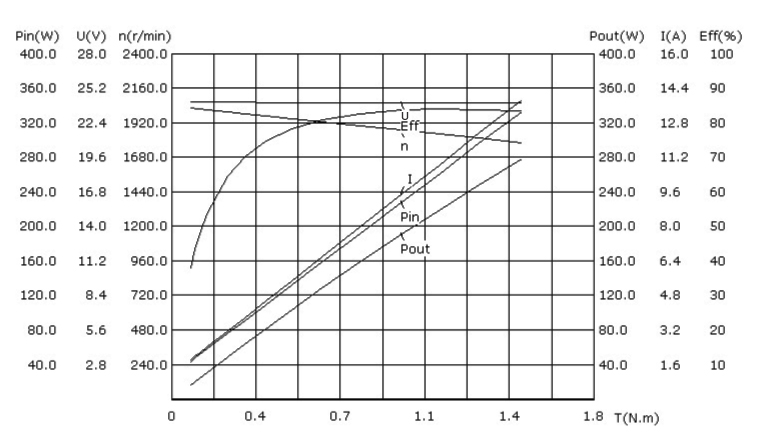
Details
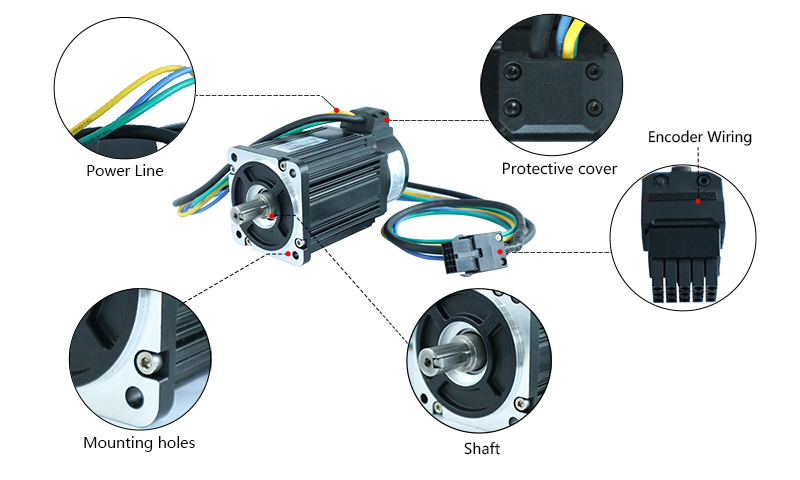
Tips: Servo Motor Position Control
DC servo motor consists of stator, rotor core, motor shaft, servo motor winding commutator, servo motor winding, tachometer generator winding and tachometer generator commutator, and the aforementioned rotor core is composed of silicon steel punching sheet by laminating and fixing on the motor shaft, which is used in various digital control systems as the actuator drive and the power drive that requires precise control of constant speed or speed change curve.
Servo motors are positioned mainly by pulses. When the servo motor receives a pulse, it rotates one angle corresponding to one pulse, thus realizing displacement. Since the servo motor itself can send out pulses, every angle rotated by the servo motor will send out the corresponding number of pulses, so that the pulses received by the servo motor form a echo, or a closed loop. In this way, the rotation of the motor can be controlled very accurately, so as to achieve accurate positioning up to 0.001 mm.