Industrial non-contact infrared temperature sensor with high performance sensor probe can detect reflect light. IR temperature sensor can measure temperature continuously, millisecond response speed, small in size, suitable for narrow working conditions.
Specification
Model |
ATO-BRW600-400A |
Measurement Range |
0 ~ 100℃, 200℃, 300℃, 400℃, 500℃, 600℃, 700℃, 800℃, 900℃, 1000℃, 1200℃ (Optional) |
Object Distance Ratio |
20:01 |
Power Supply |
10 ~ 30VDC / 5 ~ 30VDC |
Accuracy |
±2% or ±2℃ |
Emissivity |
0.95 |
Signal Output |
4–20 mA or RS485 (Optional) |
Working Temperature |
85℃ |
Response Time |
200 ms |
Response Wavelength |
8 – 14 μm |
Maximum Current |
< 50 mA |
Storage Temperature |
-40 ~ 85℃ |
Ambient Temperature |
0 ~ 60℃ (Better performance at 0 ~ 50℃) |
Relative Humidity |
10 ~ 95% RH (No condensation) |
Protection Grade |
IP65 |
Dimension |
L119mm × φ18.7mm |
Shell Material |
Stainless Steel |
Weight |
1 kg |
Feature
- Silicon-Based Microtechnology: Non-contact infrared temperature sensor has a highly sensitive temperature coefficient and excellent infrared detection for accurate and natural temperature measurement.
- High-Speed Processing Chip: Built-in high-performance processor ensures rapid signal conversion for more stable and precise data output.
- Strong Anti-Interference: Designed with robust EMI resistance, allowing stable operation even in complex electromagnetic environments.
- Stainless Steel Housing: Made from premium 304 stainless steel, offering excellent corrosion resistance and durability in high-temperature environments.
Dimension (Unit: mm)
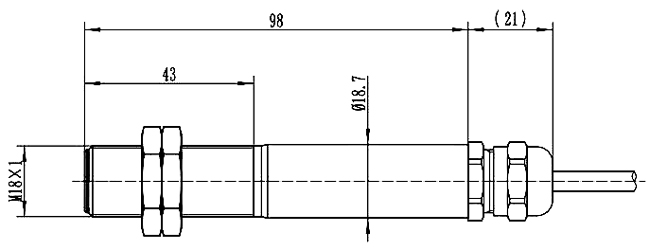
Wiring
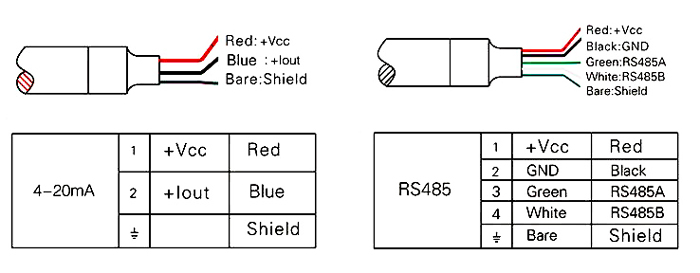
Detail
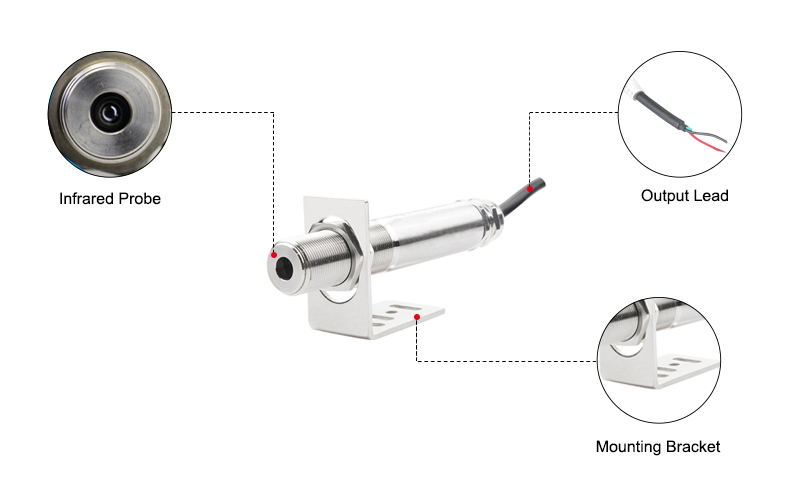
Application
Applied in power equipment, medical field, process and production industries, metallurgy, petrochemical, electric power, light industry, textile industry, food industry, national defense, and scientific research fields.
Tips: Infrared temperature sensor for electrical power system
Many equipment accidents in the power system are initially caused by abnormal heating, and many substations with a large number of electrical equipment have implemented unattended working conditions. If these equipment are under high load for a long time, the temperature will often rise, which is often invisible to the human eye at first, eventually leading to thermal failure when the temperature increases cumulatively.
The use of infrared temperature sensors to monitor the temperature of electrical equipment in operation can directly observe whether there is a suspected fault in the equipment. By combining with the Internet of Things, cloud computing, and other technologies, the monitored equipment temperature and other abnormal events can effectively help power workers solve thermal faults and defects in the operation of substation equipment, and ensure the healthy operation of electrical equipment.