What is Pressure Gauge Working Principle?
The pressure gauge we usually refer to is an instrument that uses elastic elements as sensitive elements to measure and indicate pressure higher than the environment. It has a wide range of applications. Almost all modern industrial processes and scientific research fields use pressure gauges, such as heat pipe networks, oil and gas transmission, water and gas supply systems, and street vehicle maintenance stores that we see every day. Pressure gauges can be seen everywhere. Speaking of this, you may not know much about the working principle and structure of the pressure gauge, right? Today, let's learn about the working principle of the pressure gauge and other details.
How does a pressure gauge work?
Simply, the working principle of the pressure gauge is actually through the elastic deformation of the sensitive components (such as Bourdon tubes, bellows, bellows) in the watch, and then the conversion mechanism of the movement inside the watch transmits the pressure deformation to the pointer, causing the pointer turn to indicate the change of pressure, so as to achieve the purpose of measuring pressure. The pressure gauge is usually composed of an overflow hole, a pointer, and a glass panel. The overflow hole is mainly used to prevent the internal pressure of the gauge from being released to the outside through the overflow hole to prevent the glass panel from bursting if the Bourdon tube bursts.
Pressure types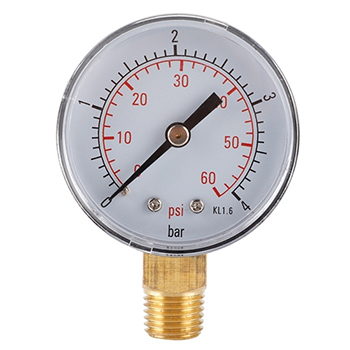
In fact, pressure gauges have been developed nowadays, and there are many types of them. From the medium, they are divided into ordinary medium and special medium, and from the application, they are divided into conventional series and digital series. Pressure gauges are classified into Bourdon tube (spring) pressure gauges, bellows pressure gauges, and diaphragm pressure gauges according to their structural principles. The most widely used is the spring pressure gauge.
The pressure gauge is mainly composed of a spring tube, a gear transmission amplification mechanism, a pointer, a dial, and a casing. The spring tube is a hollow metal tube bent into an arc shape, and its cross-section is made into an oblate or elliptical shape. One end of it is closed, and the other end is welded on the fixed support and communicated with the pipe joint. When the spring tube is under the pressure of the medium, its movable end will stretch out, and the transmission mechanism will drive the pointer to rotate, and the pressure of the medium will be indicated on the dial.
When reading the pressure gauge, keep your eyes on the scale of the dial, and the eyes, pointer, and scale form a straight line perpendicular to the dial. After the pressure is stable, read the degree; if the pressure is unstable and the pointer swings, you should read it several times (that is to say, read the pointer the maximum and minimum values), then take the arithmetic mean.
When reading the pointer pressure gauge, it is generally estimated to read 1/5 of the minimum division value. As shown in the figure below, the minimum scale of the pressure gauge is 0.2MPa, and the estimated reading is 1/5 of 0.2MPa, which is 0.04MPa. The final pressure gauge reading can be estimated as: 3.28MPa.
In the range selection of pressure gauges, when measuring stable pressure, the maximum working pressure should not exceed 2/3 of the range; when measuring pulsating pressure, the maximum working pressure should not exceed 1/2 of the range; when measuring high pressure, the maximum working pressure should not exceed 3/5 of the range; in order to ensure measurement accuracy, the minimum working pressure should not be lower than 1/3 of the range.
According to the above principle, after calculating a value according to the maximum pressure to be measured, select a value slightly larger than this value from the pressure gauge range series to be the selected range.
Buying guide
The selection of pressure gauges first needs to meet the requirements of the buyer's production process. For example, if a company wants to use pressure gauges in ammonia pressure measurement, ordinary pressure gauges are not suitable, because the spring tube of ordinary pressure gauges is made of copper alloy or alloy steel, while the spring tube of the ammonia pressure gauge is made of carbon steel and stainless steel, and the chemical reaction between ammonia and copper will have certain dangers, so ordinary pressure gauges cannot be used for ammonia pressure measurement. Therefore, the correct selection of the instrument type according to the process requirements is an important prerequisite to ensure the normal operation and safety of the instrument.
Selection example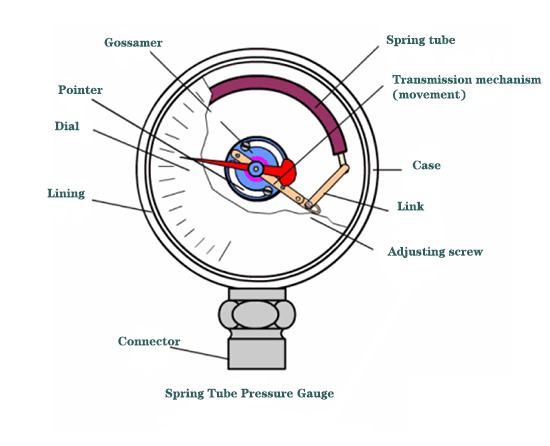
When used to measure special media such as viscous or acid-base, diaphragm pressure gauges, stainless steel spring tubes, stainless steel cores, stainless steel shells, or bakelite shells should be used.
According to the different media to be measured, there should be a specified color code on the pressure gauge, and the name of the special media should be indicated. The oxygen meter must be marked with the words "no oil" in red, the hydrogen with a dark green underlined color code, and the ammonia with a color code. Yellow underline color scale and so on.
When installing against the wall, you should choose a pressure gauge ( with edges; when installing directly on the pipeline, you should choose a pressure gauge without edges; when directly measuring gas, you should choose a pressure gauge with a safety hole behind the case. Considering the position of the pressure measurement and the convenience of observation and management, the diameter of the watch case should be selected.
Measurement accuracy
According to the maximum absolute error allowed by the process production and the selected instrument range, calculate the maximum quoted error allowed by the instrument, and determine the accuracy of the instrument in the accuracy grade stipulated by the state. Generally speaking, the more precise the instrument selected, the more accurate and reliable the measurement result will be. However, it cannot be considered that the higher the precision of the selected instrument, the better, because the more precise the instrument is generally, the more expensive it is, and the more troublesome it is to operate and maintain.
Measuring range
In order to ensure that the elastic element can work reliably within the safe range of elastic deformation, when selecting the range of the pressure gauge, it is necessary to leave enough room according to the size of the measured pressure and the speed of the pressure change. Therefore, the upper limit value of the pressure gauge should be higher than the maximum pressure value possible for in-process production.
According to the "Technical Regulations for Chemical Automatic Control Design", when measuring stable pressure, the maximum working pressure should not exceed 2/3 of the upper limit of measurement; when measuring pulsating pressure, the maximum working pressure should not exceed 1/2 of the upper limit of measurement; When measuring high pressure, the maximum working pressure should not exceed 3/5 of the upper limit of measurement. Generally, the minimum value of the measured pressure should not be lower than 1/3 of the upper limit value of the instrument. So as to ensure the linear relationship between the output of the instrument and the input.