How to Test Heavy Duty Connectors?
Heavy duty connectors play a critical role in industrial applications, ensuring the reliability of equipment and systems. Regular testing is essential to ensure the proper functioning of the heavy duty connectors. This article by ATO store details how to test heavy duty connectors, including connection methods, test preparation, test methods, and precautions.
Connection Method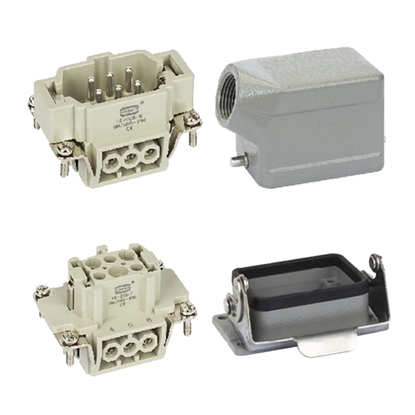
Before testing heavy duty connectors, it is important to first understand how heavy duty connectors are connected. Heavy duty connectors are usually designed with pins and slots, but the specific connection method may vary by model and manufacturer.
- Pin and Slot Connection: This is the most common connection where one heavy duty connector has pins and the other heavy duty connector has slots. The pins are inserted into the slots to ensure proper alignment and then locked.
- Threaded Connection: Some heavy duty connectors have a threaded design in which the connectors are connected by rotating the threads. This type of connection is typically used for liquid or gas transfer.
- Crimp Connection: Crimp heavy duty connectors make a connection by pressing a conductor into the port of the connector. This type of connection is typically used for wires and cables.
- Clamping Connection: Clamping heavy duty connectors use a clamp or slot to hold the connectors together, ensuring a stable connection.
- Plug Connection: Plug connectors allow multiple harnesses or cables to be plugged into a single heavy duty connector and are typically used for multi channel data transmission.
Knowledge of connection styles is critical to proper testing and troubleshooting, as different connection styles may require different test methods.
Test Preparation
Before testing a heavy duty connector, several necessary preparations need to be made to ensure the accuracy and reliability of the test.
Ensure that the appropriate tools and equipment are available to perform connector testing. Test instruments, such as multimeters, oscilloscopes, voltmeters, etc., for measuring electrical properties. Cleaning tools such as electronic grade cleaning solvents and brushes for cleaning pins and slots. Replacement heavy duty connectors so that failed connector sections can be replaced during testing. Appropriate connecting cables for connecting the test instrument to the heavy duty connectors.
Selection of an appropriate test environment to ensure that the test process is free from external interference. When testing heavy duty connectors, a relatively clean work area is usually required to prevent dirt or contaminants from entering the connector.
When testing heavy duty connectors, follow appropriate safety measures, including disconnecting the power supply and complying with relevant electrical safety standards. Ensure that testers have the necessary safety training and equipment. Refer to relevant specifications and documentation to ensure that the testing process complies with standards and manufacturer's recommendations. This helps to ensure the accuracy of good quality connectors and consistency of testing.
Test Methods
Conducting heavy duty connector testing requires following appropriate methods to assess performance and reliability.
Electrical Testing: Using a multimeter or resistance meter, test for continuity between conductors within the heavy duty connector. Ensure that current can flow freely through the connector and that there are no breaks or shorts. Using a voltmeter or oscilloscope, test the voltage transfer performance of the heavy duty connector. Ensure that the voltage is stabilized in the heavy duty connector with no significant voltage drop. Test the current transfer capability of the heavy duty connector to ensure that it can withstand the expected current load. Test the insulation between heavy duty connectors using an insulation test instrument to ensure there is no leakage or insulation failure.
Mechanical Testing: Perform multiple tests of plugging and unplugging heavy duty connectors to simulate actual usage. Check the locking mechanism and stability of the heavy duty connectors to ensure that the heavy duty connectors can withstand repeated insertion and removal. Use a shaker or vibration test equipment to simulate the vibration environment, and check whether the heavy duty connector can maintain a stable connection under vibration. Use shock test equipment to simulate a shock environment to check whether the heavy duty connector can maintain a stable connection under shock.
Sealing Performance Test: Expose the heavy duty connector to liquid to test its waterproof performance. Check if the heavy duty connector can maintain electrical performance in a wet environment. Test the dustproof performance of heavy duty connectors by simulating a dusty environment using dust or dust particles.
Temperature and Humidity Testing: Cycle the heavy duty connector through different temperatures to simulate the effect of temperature changes on the performance of the heavy duty connector. Test heavy duty connectors in a high humidity environment to evaluate their moisture resistance.
Precautions
When testing heavy duty connectors, the following key points need to be noted to ensure the accuracy and safety of the test.
- Follow Safety Standards: Always follow applicable electrical safety standards during testing to ensure the safety of testers.
- Clean with Care: If heavy duty connectors need to be cleaned, use appropriate cleaning tools and solvents. Handle with care to avoid damaging connectors.
- Record Test Data: Record test results and data for comparison and follow up. This data helps detect trends in performance degradation and failures.
- Maintain Connector Integrity: Minimize the number of times heavy duty connectors are plugged and unplugged during testing to maintain their integrity and reusability.
- Replacement Parts: During testing, have replacement heavy duty connector parts on hand to be swapped out when needed. This helps minimize test interruptions and production downtime.
- Periodic Testing: Perform heavy duty connector testing regularly, not just when a problem occurs. Preventive maintenance can prevent future failures.
- Follow Manufacturer Recommendations: Follow the high precision heavy duty connector manufacturer's recommendations and specifications to ensure proper testing and maintenance.
With regular testing, the performance and reliability of heavy duty connectors can be evaluated, reducing the occurrence of failures and production interruptions. Following proper test methods and precautions will ensure accurate and safe testing and maintain the sustainable performance of heavy duty connectors. It is important to include heavy duty connector testing in your preventive maintenance program to ensure the long term reliability of your industrial systems.