Air Compressor Different Types & Applications
An air compressor is a device that converts power into potential energy stored in compressed air. By one of several methods, an air compressor forces more and more air into a storage tank, increasing the pressure. Air compressors are widely used in industrial production to provide power for production. After the air is compressed, it can be used as power, machinery and pneumatic tools, as well as control instruments and automation devices. Ranging from the drive of various pneumatic machinery to the national defense, the power converted by the air compressor is used.
There are many types of air compressors. The classification is as follow:
Piston Air Compressor
Piston air compressors are among the earliest compressors, and it is still the most commonly used and very efficient type of air compressor. The advantages of piston air compressors are simple structure, long service life, and easy realization of large capacity and high pressure output. The disadvantage is that the vibration noise is large. Since it exhausts intermittently and has pulses at the output, it requires air tanks.
When the piston air compressor driver starts, the reciprocating piston in the cylinder moves to the right, the pressure in the left cavity of the piston in the cylinder is lower than the atmospheric pressure. The suction valve is opened and the outside air is sucked into the cylinder. This process is called the compression process. When the pressure in the cylinder is higher than the pressure in the output air line, the exhaust valve opens. The compressed air is sent to the air pipe, and this process is called the exhaust process. The reciprocating motion of the piston is formed by the crank-slider mechanism driven by the motor. The rotary motion of the crank is converted into sliding - the reciprocating motion of the piston.
Piston compressors are widely used. It can compress air as well as gas with very little modification. Piston compressors are the only design capable of compressing air and gases to high pressures suitable for applications such as breathing air compressors. Reciprocating compressor configurations can range from single-cylinder configurations for low pressure/small capacity applications, to multi-stage configurations capable of compressing to very high pressures. In a multi-stage compressor, air is compressed in stages, increasing the pressure in stages.
Rotary Screw Air Compressor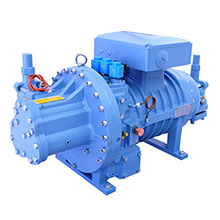
Screw air compressors are positive displacement compressors with a piston in the form of a screw. It is the most widely used type of compressor today. The main components of the screw compression element are male and female rotors, which move close to each other, gradually reducing the volume between them and in the cavity. The pressure ratio of the screw type depends on the length and profile of the screw and the shape of the exhaust port. The screw element is not equipped with any valve, and there is no mechanical force that creates an imbalance. It is therefore possible to work at high shaft speeds.
Rotary Vane Air Compressor
The vane compressor is mainly composed of three parts: the body (also known as the cylinder), the rotor and the vane. The rotor of the sliding vane compressor is eccentrically arranged in the cylinder, and a plurality of longitudinal grooves are opened on the rotor, and sliding vanes that can slide freely along the radial direction are installed in the grooves.
Since the rotor is eccentrically arranged in the cylinder, a crescent-shaped space is formed between the inner wall of the cylinder and the outer surface of the rotor. When the rotor rotates, the sliding vane is thrown out of the groove by centrifugal force, and its end is close to the inner wall of the machine body, and the crescent-shaped space is divided into several fan-shaped chambers by the sliding vane-basic displacement. Within one rotation of the rotor, the volume of each element will gradually increase from the minimum value to the maximum value, and then gradually decrease from the maximum value to the minimum value. With the continuous rotation of the rotor, the basic displacement changes over and over again following the above rules.
Centrifugal Air Compressor
The principle of the centrifugal air compressor is that the impeller drives the gas to rotate at a high speed, so that the gas generates centrifugal force. Due to the diffused flow of the gas in the impeller, the flow rate and pressure of the gas after passing through the impeller are increased, and compressed air is continuously produced.
When the gas enters the impeller of the centrifugal air compressor, under the action of the impeller blades, under the action of the rotating centrifugal force, when the impeller flows into the outlet of the impeller, it rotates at a high speed together with the impeller, and is diffused by the impeller, its pressure The energy and kinetic energy increase and the gas enters the diffusion pressure. After the device, the kinetic energy is further converted into pressure energy, and the gas flows through the bend and recirculator to the next impeller for further compression, so that the gas pressure meets the requirements of the process.